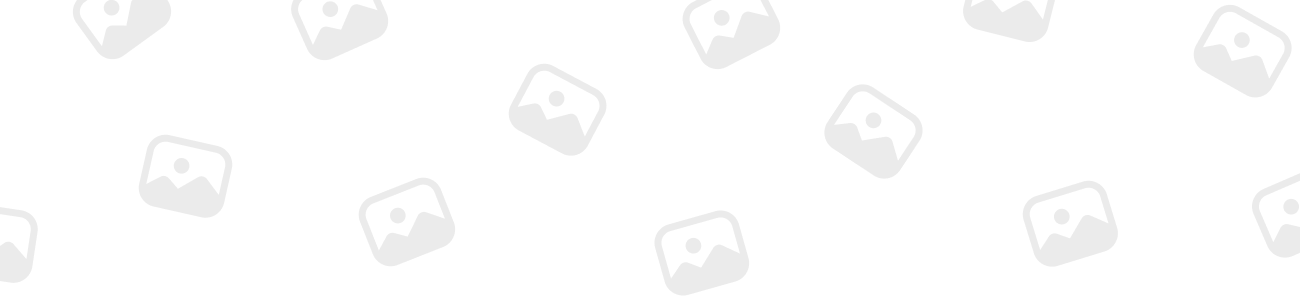
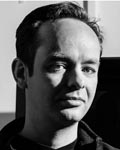
Richard Wills
Forum Replies Created
-
Richard Wills
MemberFebruary 3, 2020 at 11:33 pm in reply to: That old age questions, how the hell do I cut composite boardsIs no-one going to say Steeltrak?
I know that the pizza wheels cause subtle roll on the front edge (and, yes a couple of K purchase price). But now you’ve got me thinking about using the stanley blade and snapping on the work bench.
If you don’t have a vertical cutter, then a javelin bar gives controlled cutting (I’ve used it a few times when the pieces need more than a 2100mm cut). Also puts far less strain while cutting, and grips very well, and is oretty straight.
Never got on with the double Noga deburr, but use the single swivle all the time with aluminium.
As an aside, the carpenter/handy chap in the building has recently got himself a Mafell track saw. Damnd thing, on extraction, rips through a sheet of ply or MDF, with virtually no dust. Very well designed, and with some tinsell, might be another option. But, I can live with lightly rolled edges this week.
Just popped tendon in my right index finger, have 45 photograpic prinst, on Dibond to mount and trim tommorow, for an exhibition Thursday. Trying to work out safest accurate method to get the mounting and trimming done, pottentially with the help of office staff (no apprentices, Yet), that won’t have people (alu) paper cutting themselves.
Sorry for typos, trying to relearn typing, and…
-
Richard Wills
MemberNovember 27, 2019 at 10:05 pm in reply to: Free to a good home ! Excalibur cutterIf you’ve got the space and the time, you’ll have a lifetimes worth of spares, and an extra couple of production stops.
A local fabrication firm, and you could have 8′ in and out, or a panel cutter in the clean and dirty spaces.
-
Richard Wills
MemberOctober 28, 2019 at 7:11 pm in reply to: What is the best type of flooring to have for wrapping vehicles on?We laid those in our last place, partly because the floors were uneven and frankly knackered. Moved 6 monthes ago to the second floor of an ex-council building, and took them with us (production is three smallish offices converted into one).
Only drawback, was production running until the week of the move, and starting again shortly after. That was the small flaw in the plan, got around by taking sections out, wheeling machines and tables about, then laying back down in phases.
Heavy buggers, and a real pain to lay if you don’t get them dead lined up (and decent gloves), but simple to cut down with a stanley knife (or keencut), and very forgiving of sheet materials resting on them, as well as shiny devices dropped on them.
Vaccuum and mop regularly, and they are not a dust problem.
-
Only for prepping paintwork, prior to vinyl hanging, as per 3M recommendations.
Used neat the rest of the time, and the smell acts like a magnet to certain other occupants of the building. As a kid, I remember being told that vodka smells like paint stripper. No, paint stripper smell like good vodka.
-
I’ve just done five windows (1.5×2.5m) and a door. Three of the windows get a couple of hours direct sun, the door and two of the windows, strong sunlight for much of the day.
Followed the 3M cookie method, using fairy and water. draped over with bubble wrap. After 4 hours, was able to get strips about the size of a playing card. More juice added, and left covered over night.
Next morning, four of the windows came off in one piece, with virtually no resistance. One of the windows and the door were a different matter. It didn’t help that the door was open most of the day, and the wind was drying the juice. Gentle persuasion with a razor blade, with very regular re-application of juice brought most of the frosting off, in blade width strips. Corners were a bugger.
Now, if anyone knows how to remove the knackered solar film on the outside… Also probably 15 years old.
-
Human vision is particualrly sensitive to subtle shifts in shades of neutral tones, which can be the slightest deviation from neutral in the magenta to green or yellow to blue, or cyan to red axes. Changes in substrate white points, laminates, inks will all have a clearly visible effect, as will temperature and humidity when the inks are laid down.
If you really want to get colour under control, then you do need to go down the profiling route. Manufacturer’s profiles will get you in the ball park, but, particularly if you are applying laminates, then you eventually will need profiling kit.
X-rite’s i1-Pro, with profiler software lets you print calibration targets. Let them dry as you would normally, then apply laminate, then read the target. Now you have a profile for the vinyl / laminate combo. You can take things further – say you’ve got a client who’s just picked up half a dozen ex-Royal Mail vans, and wants new vinyl – place the laminated vinyl target over a rich red base, and measure the target (OK, that’ll probably never work), but you could make profiles over ice white v’s cream, v’s silver, and control the neutral colour shift.
Quality inks, quality media and laminates are capable of profiling without TooMuch effort, though you’re looking at a couple of grand for the kit, and as many hours as it takes. Having said that, illuminant metamerick mismatch (the effect of trying to judge colours under something like sodium vapour lamp, or cheap flourescent) will almost always skew the neutral balance, because the light is yellow, or green…
Or… If you are using the same printer / ink / media / laminate combo’s, there are firms out there who will help make a custom profile for you – probably less than a couple of hundred pounds, and if you buy everything from one supplier, then they should offer this for you.
HTH – feeling slightly happy that I’ve just resurrected two of our printers this week, when I was planning to skip them, rather than move them to new premises.
-
If you want to get really serious, then these are what we use in our print room
http://www.graphictec.co.uk/Overhead_Co … s/1918.htm
We’re predominantly fine art printing, but a lot of what we do has cross overs with sign making.
I wouldn’t dream of buying these if I didn’t have a fair sized investment in kit from Eizo and x-rite. -
Richard Wills
MemberJanuary 14, 2019 at 11:30 pm in reply to: New Member introduction. hope its in the right place.Hello Andrew,
Just about to get one as well – in a similar boat, so don’t feel alone.
Great thing about this board – seemingly silly questions are the ones you don’t ask.
-
As per Neil, it depends on the level of conservation wanted, and the budget available. I’d suggest that you ask the museum how long they would like to preserve the original artifacts, and then suggest they seek advice from an expert – most likely a larger museum, or a professional conservator.
If the museum is serious, then you should politely forward the job back to them.
-
Richard Wills
MemberDecember 11, 2018 at 10:30 pm in reply to: Cut vinyl lettering – an indictation of cost pleaseThanks, I look forward to seeing if I can afford to go top notch.
Most likely, all design will be done in illustrator, as most of the staff who’ll be generating files are reasonably experienced with Adobe SW, and we’re not looking at complex designs (yet…)
Martin, did you mean metamark M7? Can’t find your thread on tiny text.
-
Richard Wills
MemberDecember 11, 2018 at 6:30 pm in reply to: Cut vinyl lettering – an indictation of cost please -
Richard Wills
MemberDecember 11, 2018 at 4:45 pm in reply to: Cut vinyl lettering – an indictation of cost pleaseThanks Chris, I’ll claim sticker shock reduced my ability to read. I’ve always preferred to buy once, rather than cheap.
-
Richard Wills
MemberDecember 11, 2018 at 3:04 pm in reply to: Cut vinyl lettering – an indictation of cost pleaseThanks Steff, are the Suma’s wildly better than the Graphtec, for what we’re after – this won’t be running every day.
A lot of the text we’ll be working with will be nearer 25 – 100mm high, but I have a colleague who likes small text, so I’ll let her learn how to weed small letters (fortunately, house style is sans-serif).
Already have laminator, and laminate and mount prints to aluminium and DiBond, with a couple of 8×4 benches, and plenty of light boxes (do they help for weeding?)
Most of the text will be a mid grey, as well as potentially some out from window frosting (aware that 24" isn’t totally ideal, but can design the graphics with feature spacing).
We may be moving into a rabbit warren of a new space, so will need signage and info all round. Rather than print and mount onto forex etc, figured It was time to go straight to the wall. That and the ability to have text on the gallery walls at relatively short notice, is what’s tipping the balance (but not quite to £2k). If colleagues want last minute text, then they can experience the joys of weeding, until they start getting their orders in, in a timely fashion.
-
Richard Wills
MemberDecember 11, 2018 at 12:15 pm in reply to: Cut vinyl lettering – an indictation of cost pleaseSo, again thank you for advice so far.
Looking to get something like a CE6000-60, for a couple of usages, mostly lettering. I imagine that the size of text we could go down to would be dependent on the font, and grade of vinyl used – probably nothing smaller than 10mm high, to go onto glass, painted wall and Forex or DiBond, for internal signage.
Thanks.
mod-edit
-
Richard Wills
MemberSeptember 21, 2018 at 7:55 am in reply to: Cut vinyl lettering – an indictation of cost pleaseFor the first time in months, I’ve not had to turn on the aircon this morning.
-
Richard Wills
MemberSeptember 20, 2018 at 7:56 pm in reply to: Cut vinyl lettering – an indictation of cost pleaseThis is a trade supplier – six miles down the road, so we usually get the graphics biked over.
I understand rush fees happen, but only on the text panel this time. We didn’t even specify precise shade of grey, nor brand of vinyl – had assumed that a mid to dark grey vinyl would be a stock item for a mid to large sized firm. SO, perhaps they don’t want the work. (details on an earlier message were from a response from our previous supplier)
I’m photographic by background, but a lot of what I do has overlaps with the sign trade. Any suggestions for file format export from indesign (or illustrator?), to make cutting simple for a supplier?
Or, given our annual spend on cut vinyl, should I follow my thoughts on taking this inhouse with something like a graphtec ce6000-60? We’re not making signs, and most of our text panels top out at A1.
We’re B2B and B2C, specialising in photographic printing and exhibition production, with a reasonable gallery, a couple of miles from Parliament.
Thanks, both for reminding me that I may be thinking in a similar way to one or two of my clients, and for your responses.
-
Richard Wills
MemberSeptember 20, 2018 at 5:22 pm in reply to: Cut vinyl lettering – an indictation of cost pleaseFair enough – it was first thing this morning when we contacted them – Other elements were quoted at total £100 plus vat, which is on a par with what we’ve been charged previously.
File as PDF from indesign
-
Richard Wills
MemberSeptember 20, 2018 at 4:18 pm in reply to: Cut vinyl lettering – an indictation of cost pleaseKeep upping the price until the job goes away.
Anyone interested in this – needed for Tuesday, and there are some additional larger text elements – on top, as well as a couple of lines, same vinyl in reverse for front door (72pt lettering)
-
Richard Wills
MemberMarch 13, 2018 at 3:59 pm in reply to: Vinyl not sticking to painted wall surfaceI’ve some samples of Canvastex, and a similar generic on the wall in my print room (paint is Munsell N7 – high quality eco matt), and they’re kind of losing their grip. They went up a year after the wall was painted, but not 3M’d, so, I’d still go for the surface prep, for anything I wasn’t wanting to revisit…
All our prints are aqueous, rather than solvent, but I don’t suspect this will have a huge impact on the adhesive. But they are all designed to come off cleanly, just not of their own accord.
-
Richard Wills
MemberMarch 13, 2018 at 2:42 pm in reply to: Vinyl not sticking to painted wall surfacequote Hugh Potter:there was a 3M (I think) demo on here somewhere which while I thought was a bit OTT, but basically using a water / Iso mix you wipe the wall down etc.Hung a show in our gallery a couple of weeks ago, with large sections of Canon repositional matt vinyl, matt eco friendly paint on the walls. Sections of the wall that had been recently painted were mopped down three times with IPA / Water mix. Some of the vinyls were larger than anticipated, and went onto walls which had not been painted for months, and only got a quick, single wipe down with the IPA/Water mix. A week later, the vinyl is lifting, but only on the insufficiently treated areas.
So, I can say with confidence that the 3M method is not OTT, and is worth the extra prep time.
-
A fantastic bit of kit, gone to a good home, at a bargain price.
On our rev.D, I’ve had excellent results using a 2033 patch chart, but without the automated table, it’s a pain to profile each combination of paper laminate and substrate, though it is worth it.
There’s a discussion here http://forum.luminous-landscape.com/ind … #msg988447 about optimal patch numbers for the best colour fidelity. Written by people wanting the best quality output for photography, still, I suspect, relevant for you.
-
I was rather hoping that someone would say there was a way to get a cutter to trim heavy paper – we print photographic exhibitions and other work on a Canon 8400 aqueous, and I would love to get a machine in to trim prints, so we could cost effectively offer smaller prints than our base A3 size.
We cut everything by hand, and don’t have the space (or budget) for a big flatbed cnc cutter, but could fit in a 44" (or ITRO) cutter. From what I have read to date, Roland, Graphtec etc are not deigned to cut the heavier papers, but I would love to be wrong!
-
If the edges are very sharp when cut with a knife, then you may be looking at GatorBoard.
Very dense and hard for a foam board. I last got some from http://www.johnpurcell.net/
-
Richard Wills
MemberNovember 29, 2016 at 6:20 pm in reply to: London Kapa Mount suppliers who are likely to carry stock?Thanks James – Hoping for a good news phone call from the supplier in the morning – other wise, will give you a shout.
Much appreciated!
-
Richard Wills
MemberSeptember 28, 2015 at 1:17 pm in reply to: London Supplier of UHB tape urgently needed – help please?Thanks Jon.
Managed to borrow some 3M bond tape from a mounting company in Farringdon – The lovely people at A Bliss came to our rescue.
If you ever need a fine art mounting service, all sorts of options, look them up – no connection with them, other than a happy competitor! -
Richard Wills
MemberMay 26, 2015 at 8:30 am in reply to: reverse printing photos and laying on acrylicGenerally reverse face is printed to a glossy photopaper, and attached to the back of the perspex using an optically clear mounting film (drytac facemount adhesive (really horribly expensive)).
You’ll want to be working in the most dust free space imaginable!Then mounted to a sheet of either DiBond, or aluminium (the solid silver backing). Indasol UHB 9120G with surface primer to bond an aluminium sub frame / z-hanger to the back.
-
I suspect that your RIP lets you import custom profiles. Depending on the number of media you use, one option would be to purchase something like the http://www.colormunki.com/product/show? … _type=true designer version of the x-rite colormunki product.
Allows you to profile printers (RGB and CMYK), as well as screens. Costs around £400 to buy, and then of course you have to learn how to use it(not hard), and take time to use it. Might be cheaper than buying (learning, setting up etc) a new RIP. And definitely cheaper than a complaining customer!
It gives you have option of profiling up any media that you want to try / use, with or without laminates. Takes pretty much all of the guess work out of laying down ink.
The Munki (Blo0dy awful name) is the baby sister of the i1 pro, which is a lovely beastie, capable of even greater control, but atleast 5x the price.
-
Richard Wills
MemberAugust 15, 2014 at 4:10 pm in reply to: Matt black removable vinyl for temporary indoor useThanks Chris/Chris,
Will get a sample of the metamark, as well as Avery 500. The more I look at this, the more I think that we should break the mould and go for a high key cinema feel.
-
quote Kaye Elsender:It was on some kind of mother and baby site about not putting vinyl decals in baby’s rooms because of the toxins it can produce.
The sort that would go mad if they ever googled "Dihydrogen Monoxide FAQ"
-
Not sure if this will help, but we’ve had real problems in the past with inexpensive "foamex" PVC – the material fits within the manufacturer’s spec of +/-10% – the difference of 1mm in thickness across the width of an eight foot sheet caused every laminator run to fail.
These days, I’ll only ever order Forex, which is a complete PITA, now that RHG don’t supply it.
So, it could be the substrate not being flat that is helping the problem.
-
Lion Picture supplies are pretty good for these sorts of things – I believe these are the blades you are looking for: http://www.lionpic.co.uk/product/KEENCU … 205,0.aspx
How do you find the Evo2? I’m tempted to upgrade our Javelin just to get the one handed lift/close mechanism.
-
Richard Wills
MemberAugust 1, 2013 at 6:59 pm in reply to: just about had enough of Robert Horne / paperlinx.Credit to RHG, with the exception of no longer supplying 3A composite products, they’ve been one of my best (on account) suppliers. Deliveries on time, to our (central Brixton side road) address, with The Best Packaging of materials.
Haven’t yet needed to restock since they became paperlinks, but hope they haven’t dropped the ball.
Wrt credit cards, you can register a second address with your card provider, so that the CV2 details (the post code and address numbers bit of the card transaction verification) match your delivery address..
I won’t go into the ineptitude of one of the current DiBond / Forex suppliers drivers – would end up ranting all night (but 200yards down cold harbour lane is real fun when carrying 1/4 tonne of 8×4’s).
-
Richard Wills
MemberNovember 26, 2012 at 2:17 pm in reply to: disabling the printers colour managementyep, that is colorsync recogninsing that you’ve got Photoshop managing colour, and so it is not offering any colour management options in the Canon print dialogue.
"At the moment no matter what profile I use the print is still the same, very dark. I have only had this problem since buying the macs"
This wouldn’t be an iMac would it – the screens on them are way too bright by default, and so the prints come out dark… (Ignore that, if you’re getting dark prints from previously printed files). -
Richard Wills
MemberOctober 26, 2012 at 1:06 pm in reply to: can anyone advise with laminating foamex?quote Dave Rowland:I have to say I never noticed fluctuations in thicknessWith the Forex, I’d agree -a remarkably consistent product. Unfortunately Amari don’t seem to be able to sell enough of the Non print version, to make it worth carrying. So far, all the alternatives I’ve tried have up to ± 10% from the 5mm (and some of them do both plus .5 and – .5mm, which is enough to leave us gubbered. I’d imagine this is not so much of an issue for vinyl users, where the material can conform to the substrate?
-
Richard Wills
MemberOctober 24, 2012 at 9:18 pm in reply to: can anyone advise with laminating foamex?We’ve backed off on the pressure (jet mounter has L&R wheels – roller down, then up a quarter – half turn, so rollers are just resting on the substrate). Setting works great on kappa mount, and on the f-lux when going "down the long edge", but not along the length of the material.
Will try a couple of things in the morning:
Back off the pressure – will try that first while the protective film is still in place – the adhesive is way cheaper than the board.
Run a section of the material cut down to fit, sideways, to see If plan c will work.
Order new cut bits, cut from the long side (so three pieces rather than four from a 5×10′) and run a promo on smaller prints!
I mouth that I had tried the light touch – will try lighter.Thanks.
Ps, what is the technical term for going from the short edge / from the long side…?
-
Use a Drytac Hotpress roller laminator day in, day out. We use the JM44 and it works well.
Would like a single wheel adjustment, would be nice, and heated rollers, even more so. I believe that the latest version of the 44" (or next size up) allows for both of my wishes. Being on a first floor with no freight lift, machines over 150KG are a Real problem, so will stick with where we are.
Hotpress / Drytac customer service is great, when needed – we’ve had them pull out all kinds of stops to get work out / machines running. Being UK based helps us. -
This is something we’ve been planning – a backlit board for presenting prints to aluminium, where we have (if we’re luck) a 2mm bleed on a 36" print. We are welcoming the heat of fluorescents in the winter, but were unsure of specification of glass, to use to cut on.
Any suggestions – we’re looking at an 8×4′ table.
-
Richard Wills
MemberAugust 30, 2012 at 10:44 am in reply to: Just Purchased an Epson Stylus Pro 9800. Any Tips?Afraid the first I’d heard of it was today… seems to work with the DTP-20 photospectrometer for creating and validating proofs and profiles (a device that was discontinued 5 years ago).
Depending on which version you have, it may give costings – certainly should allow you to control the ink laydown. Pretty much all the good proofing tools are indeed rips.
Have fun with the manual.One advantage of starting with Epson genuine media (assuming it is loaded with genuine epson carts) is that the basic profiles are not bad, though can be improved upon, so allows you to have a look-see that all the parts of the printer are running properly.
One of the things I’ve found with the 9800 is that it does not like dry air -we did have ours in a room with multiple computers, and air con, and had endless nozzle clogs. Moved it to a non controlled climate, and (touch wood) hasn’t skipped a beat for the last 15 months
-
Richard Wills
MemberAugust 30, 2012 at 9:43 am in reply to: Just Purchased an Epson Stylus Pro 9800. Any Tips?We have run a 9800 for the last 6 years, through the ImagePrint Rip (we’re still on V6, and have a G4 dedicated to running it). Nice things about imageprint is that it allows you to run MK and PK without a costly swap over, and comes with a whole raft of first class profiles. Nasty thing is it costs a small fortune (for a 44" printer rip).
All the artists we print for use the Epson Premium Satin canvas – a really nice material, and the most expensive media we print on (and we’ve tried offering them all kinds of options, but they keep going back to the Epson).
WRT http://www.techno-in.com – looks like a solid proofing product, though doesn’t seem to be actively developed any more.
-
Richard Wills
MemberAugust 2, 2012 at 7:12 pm in reply to: High quality Grand format Art printing / mountingAgain, thanks Dave for a wake up re delivery, seeing how tricky it can be to get perfect sheets of 8×4 dibond from suppliers.
And Martin, in one piece is the way the artist has always presented the work. Tbh, I suspect he would not accept the work in sections.
John, looks like an interesting option, do you have experience of the quality? For this particular client we tend to run the 8300 at its maximum quality.
I’ll look further in to the details in the cold light, but given that the production costs for a 1000mm print for him can hit >£150, I suspect the restaurant might revise their plans.Thanks again for the valued advice.
-
Richard Wills
MemberAugust 2, 2012 at 4:27 pm in reply to: High quality Grand format Art printing / mountingThanks Dave, yes, to me, anything taller than I am is Big (including printers); am I not supposed to ask about Big here…?
I’m assuming (very much open to correction) that UV direct to substrate is reasonably durable (I’m picturing hoardings on Regent Street), and that there are some seriously high quality machines that can be very effectively colour managed?
If so, and given the constraints of the sizes in which DiBond is available, are there Big suppliers who focus on print quality, or should I get some rolls of "wall paper paper" and run them out here and place a laminate over the top… -
Richard Wills
MemberDecember 6, 2010 at 12:18 am in reply to: Sealing edge of laminated prints mounted on compositeWe are using a 9800 from Epson.
For some reason, I had in my mind, the need for some exotic signmaking tape. but, thinking about it, the use of the laminate added after the event would work, flattened down by a final trip through the laminator.Thankyou. Have I missed anything?
-
Richard Wills
MemberDecember 6, 2010 at 12:15 am in reply to: Keencut Excalibur 5000 or SteelTrak ST165???quote Chris Wool:quote Alan Drury:I have an Excalibur 500 and as much as I like it I struggle to get a dead square cut on 10mm foamboard. Mine is fairly old though.
Alan Dnever really got it 100% but blade quality is very important and have thrown new ones away many times.
Keencut did say that we might see better results using normal heavy duty Stanley blades, rather than their 080 blades (which I believe are designed for lighter substrates)
-
Richard Wills
MemberDecember 5, 2010 at 9:32 pm in reply to: Keencut Excalibur 5000 or SteelTrak ST165???We have the big steeltrak, and put in a couple of hours work out on it most days.
WRT the vertically challenged, there is a pull down handle that allows my 5’8" assistant to cut from the very top. works well, but sometimes gets in the way, if you forget to fold it back.Changing from the Stanley cutting head to the composite takes about ten seconds – dead easy. Keencut supply "sightstrips" for cutting foamex etc, which works really well, but can be fouled by the composite cutter on the up stroke, unless the clamp is closed. This can lead to irritating indents on the cuts on composite (we use it for trimming DiBond for mounting photos to, so finish needs to be perfect). It’s quite possible that I haven’t fitted the sight strips perfectly; each time it gets fouled, I take them off, and put new ones up.
I recently discovered that it is possible to trim a couple of mm’s off a mounted / laminated print, when cutting through the back, leaving a Perfect smooth straight cut.
It’s very simple to set to a perfect (less than .5mm deviation on a 1500mm cut), and is virtually maintenance free.I have nothing but praise for Keencut’s customer service – any time I’ve needed help, or parts, there has been a package delivered the next day, mostly without an invoice (and they are made in the UK!).
Having said all that, I did struggle (very recently) to get a dead 90 degree edge on some 10mm Forex – the room was about 12 degrees C; problem was resolved by allowing the Forex to thaw (placed on top of the hotpress for a few minutes). Have had no problems with Kapa/foamboard. Oh, and the other problem is it won’t cut an 8×4′ lengthways – the cutting track is not long enough, but then the ceiling isn’t high enough either.
-
Richard Wills
MemberOctober 5, 2010 at 10:29 am in reply to: Monitor and printer Calibration devices Advice pleaseYou might consider the Xrite ColorMunki (awful name) as an all in one package. The design version will allow you to work with CMYK printers as well as RGB (which the R1800 pretends to be).
It is based on the technology used in the EyeOne devices, but with simplified software and hardware. It should build acceptable profiles for a variety of media, and can be used in an iterative process, to fine tune.
It should also work well with most LCD screens. The key is to control the light landing on the screen (as little as possible), and the light illuminating the printed material (not too bright, and correctly "tuned" – using a desk top viewing booth from some one like GTI lighting, or Juste Normlicht will help. The better the screen (my preference would be the Eizo Coloredge range), the more accurate the proofing, provided you have the correct working lighting.
Welcome to colour management.
-
A dedicated film scanner will do a better job than any of the consumer flat bed scanners. Try finding a second user Nikon Coolscan 4000, or even better, a 5000. Either of these will take a bulk loader for twenty or so mounted 35mm frames. The 5000 certainly has digital ice (dust and scratch remover), and I think the 4000 does as well. (D-Ice can be a but funny with Kodachromes). Load up a batch, and leave them to run over night.
Having said all that, if the viewing is only for "on screen" or small print, then the Epson V600 (or older 750) will do an OK job – you just have to load up the frames into the holders. Watch out for the focusing on some of the older card mount slides.
HTH
Richard (who has been scanning on his Imacon 949 today…) -
Richard Wills
MemberSeptember 21, 2010 at 8:49 pm in reply to: Bubbles, Bubbles and more flippin Bubbles……Method that works with our JetMounter JM44:
cut five bits of substrate – 4"x10"
raise (manual, cold) top roller, insert five bits evenly spaced across the nip, then bring down roller, until you feel it bite
raise left and right wheels, around a quarter to an eigth turn, until you feel the "slack" give
twiddle with the five "bits" to check that pressure is the same across all five bits – a bit of finger tip pressure works well with the more expensive (Drytac Facemount) adhesive.THEN
Get the micrometer out, and check across the width of the substrate. If problems come in at 5′ mark, cut down the "bubble zone" and measure the thickness across the board. Odds are that you have a batch of lemons.
We had 20 8×4′ sheets of 5mm foamaluckless delivered, which varied by almost 1mm from edges to centre. Was within manufacturers tolerances (+/-10% from memory), that was useless for our photo mounting purposes (bloody bubbles every where). Manufacturer’s rep came out, checked measurements, and said, yep, within published tolerances.Needless to say, we never ordered Mett Brartin F***luckless, from the distributor. Shame they stopped doing Forex, as we never had any problems with that, from them, and they did package the sheets up beautifully in two man carriable card.
Just got a carp batch of Forex which bubbles when laminated lengthways… fortunately the job lets us cut 41" strips and go down the short edge.
Nip down to Maplins and get a micrometer – twenty or thirty quid. Might not be up to ISO standards, but its relative measurements will show you errors in media thickness.
Sorry, rant over.
Excess pressure does not help you get an even lamination (in my very limited experience). Problems with substrate can cause you hours of pain.
Oh ,and the good fellows at Drytac Hot press did recommend that we have the entry table to the laminator slightly higher than the machine, with exit table Slightly lower.